In recent years, there has been a significant advancement in the field of Artificial Intelligence (AI) and Augmented Reality (AR). These technologies have become increasingly popular and have the potential to enhance virtual experiences in various fields such as gaming, education, healthcare, and...
AI Optimizes Manufacturing Through Predictive Quality Control and Maintenance
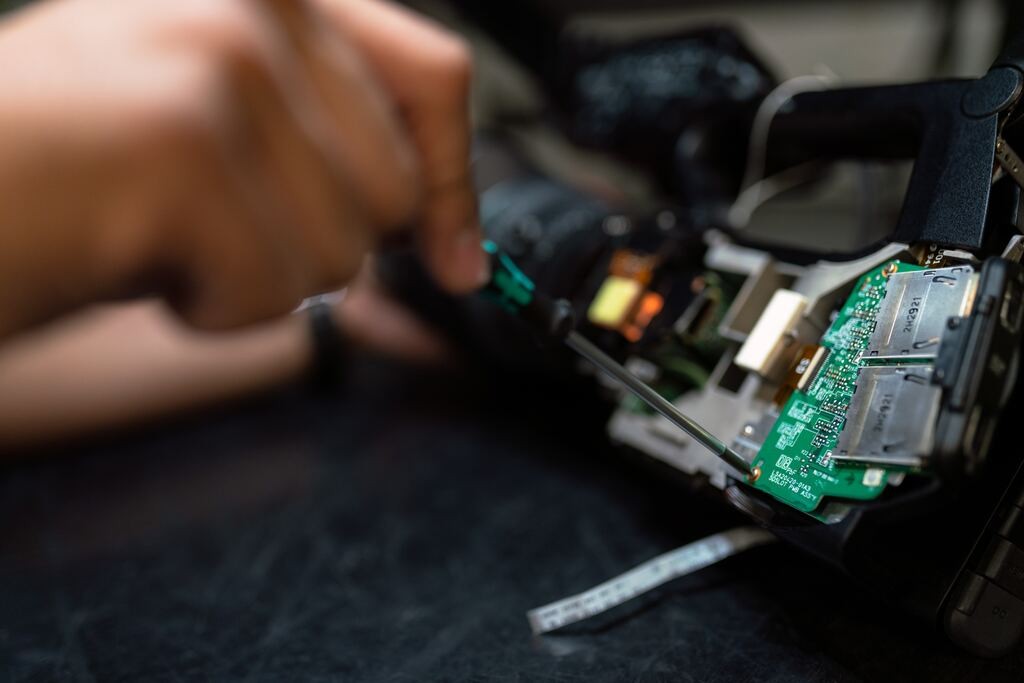
In today's rapidly evolving manufacturing industry, companies are constantly looking for ways to improve efficiency and reduce costs. One area that holds great promise is the use of artificial intelligence (AI) in optimizing manufacturing processes, particularly in the areas of quality control and maintenance.
Traditional quality control methods rely on manual inspection and sampling, which can be time-consuming, labor-intensive, and prone to human error. AI-based predictive quality control, on the other hand, leverages machine learning algorithms to analyze vast amounts of data in real-time and identify patterns and anomalies that humans might miss. This allows manufacturers to detect and address quality issues proactively, minimizing defects, waste, and rework, and ultimately improving the overall product quality.
Furthermore, AI-powered predictive maintenance enables manufacturers to monitor equipment and machinery in real-time, predicting and preventing potential failures before they occur. By analyzing sensor data, historical performance, and maintenance records, AI algorithms can identify patterns and indicators of impending equipment failure, allowing manufacturers to schedule maintenance and repairs in a more efficient and cost-effective manner. This not only reduces downtime and production losses but also extends the lifespan of equipment, optimizing its performance and reducing the need for costly replacements.
In conclusion, the integration of AI into manufacturing processes offers significant benefits in terms of predictive quality control and maintenance. By harnessing the power of machine learning and data analysis, manufacturers can proactively identify and address quality issues, minimize downtime, and optimize equipment performance. As AI continues to advance, its role in manufacturing is likely to expand, revolutionizing the industry and driving further improvements in efficiency and productivity.
AI Optimizes Manufacturing: Predictive Quality Control
Quality control is a critical aspect of manufacturing, as it ensures that products meet the required standards and specifications. Traditionally, quality control has been a manual and time-consuming process, involving random sampling and inspection of finished products. However, with the advancement of artificial intelligence (AI), manufacturers can now implement predictive quality control systems that not only improve efficiency but also reduce costs.
Benefits of Predictive Quality Control
Predictive quality control utilizes AI algorithms to analyze data from various sources, including production machines, sensors, and cameras. These algorithms can identify patterns, anomalies, and potential defects in real-time, allowing manufacturers to take proactive measures to prevent quality issues before they occur. This approach offers several benefits:
- Improved Product Quality: By identifying potential defects early on, manufacturers can make adjustments to the production process, resulting in higher quality products.
- Reduced Scrap and Rework: Predictive quality control helps minimize the number of defective products, reducing the need for scrap and rework, which can be costly and time-consuming.
- Enhanced Customer Satisfaction: Delivering high-quality products consistently improves customer satisfaction and brand reputation.
- Optimized Production Efficiency: By identifying and addressing quality issues in real-time, manufacturers can minimize downtime and optimize production processes.
Implementing Predictive Quality Control
Implementing a predictive quality control system requires the integration of AI technologies, data collection systems, and analytics tools. Here are the key steps:
- Data Collection: Gather data from various sources, such as sensors, cameras, production machines, and historical quality records.
- Data Preprocessing: Clean and preprocess the collected data to remove noise and inconsistencies, ensuring accurate analysis.
- Algorithm Development: Develop AI algorithms that can analyze the collected data and identify patterns, anomalies, and potential defects.
- Model Training: Train the AI models using historical data and labeled examples to improve accuracy and performance.
- Real-Time Monitoring: Implement a real-time monitoring system that continuously analyzes incoming data and alerts operators to potential quality issues.
- Proactive Maintenance: Utilize the insights from the predictive quality control system to schedule proactive maintenance and prevent equipment failures.
By implementing predictive quality control systems powered by AI, manufacturers can optimize their production processes, improve product quality, and reduce costs. This technology is revolutionizing the manufacturing industry, enabling manufacturers to stay competitive in today's fast-paced market.
Improving Product Quality and Efficiency
Artificial Intelligence (AI) is revolutionizing the manufacturing industry by improving product quality and efficiency. By utilizing predictive quality control and maintenance systems, manufacturers can identify and address potential issues before they impact the production process.
Predictive Quality Control
With AI-powered predictive quality control, manufacturers can analyze real-time data from various sources such as sensors, cameras, and production equipment to monitor product quality. Machine learning algorithms can detect patterns and anomalies, allowing manufacturers to identify defects or deviations from the desired standards.
By continuously monitoring the production process, AI systems can provide early warnings when a deviation is detected, enabling manufacturers to take immediate action. This proactive approach helps prevent defective products from reaching customers, reducing the risk of recalls and customer complaints.
Predictive Maintenance
In addition to quality control, AI can optimize manufacturing efficiency through predictive maintenance. By analyzing historical data and sensor readings, AI systems can predict when equipment is likely to fail and schedule maintenance activities accordingly.
By identifying and addressing potential issues before they become critical, manufacturers can minimize unscheduled downtime and optimize production schedules. Predictive maintenance also extends the lifespan of equipment, reducing repair costs and improving overall operational efficiency.
Furthermore, AI can analyze data from multiple sources, such as production equipment, supply chain, and environmental conditions, to identify correlations and optimize production parameters. By fine-tuning these parameters, manufacturers can improve product quality, reduce waste, and increase overall productivity.
In conclusion, AI-powered predictive quality control and maintenance systems play a crucial role in improving product quality and efficiency in the manufacturing industry. By leveraging real-time data and machine learning algorithms, manufacturers can detect and address potential issues proactively, resulting in higher customer satisfaction, reduced costs, and improved overall operational efficiency.
AI Optimizes Manufacturing: Predictive Maintenance
In the manufacturing industry, predictive maintenance is a critical strategy for minimizing downtime and maximizing productivity. By using AI-powered algorithms, manufacturers can anticipate and address potential equipment failures before they happen, saving time and resources.
One of the key benefits of AI in predictive maintenance is its ability to analyze large amounts of data in real-time. Sensors placed on manufacturing equipment collect data on various parameters, such as temperature, vibration, and power consumption. AI algorithms can then analyze this data to identify patterns and anomalies that indicate potential issues.
Using predictive maintenance, manufacturers can schedule maintenance activities based on the actual condition of the equipment, rather than relying on fixed schedules or reactive repairs. This proactive approach helps prevent unexpected breakdowns and reduces the need for costly emergency repairs.
Benefits of AI in Predictive Maintenance
- Increased equipment uptime
- Improved production efficiency
- Reduced maintenance costs
- Minimized risk of unplanned downtime
AI algorithms can also help manufacturers optimize their maintenance processes by providing insights into the root causes of equipment failures. By identifying recurring issues, manufacturers can take proactive measures to address them, such as modifying equipment design or implementing preventive maintenance measures.
In conclusion, AI-powered predictive maintenance offers numerous benefits for manufacturers, including increased equipment uptime, improved production efficiency, reduced maintenance costs, and minimized risk of unplanned downtime. By harnessing the power of AI, manufacturers can optimize their maintenance processes and ensure smooth operations.
Reducing Downtime and Increasing Productivity
One of the key benefits of implementing AI in manufacturing is the ability to reduce downtime and increase productivity. By leveraging predictive analytics and machine learning algorithms, manufacturers can proactively identify and address potential issues before they cause unplanned downtime.
Predictive Maintenance
AI-powered predictive maintenance systems can analyze data from various sensors and equipment to detect patterns and anomalies that may indicate a potential failure. By continuously monitoring the performance of machines and predicting when maintenance is needed, manufacturers can schedule maintenance activities during planned downtime, eliminating the need for costly unscheduled shutdowns.
By implementing predictive maintenance, manufacturers can not only reduce downtime but also increase the lifespan of their equipment. Regular maintenance and timely repairs can help prevent major breakdowns and extend the operational life of machines, resulting in improved productivity and cost savings.
Real-time Quality Control
AI can also optimize manufacturing processes by enabling real-time quality control. By analyzing data from sensors and cameras placed along the production line, AI algorithms can detect defects and deviations from quality standards with high accuracy and speed.
By identifying quality issues in real-time, manufacturers can take immediate corrective actions, such as adjusting machine settings or alerting operators to make necessary adjustments. This proactive approach helps minimize the production of defective products, reduce waste, and improve overall product quality.
Benefits of reducing downtime and increasing productivity with AI:
- Minimize unplanned downtime
- Increase equipment lifespan
- Improve operational efficiency
- Reduce production costs
- Enhance product quality
AI Optimizes Manufacturing: The Future of Production
In today's fast-paced manufacturing industry, artificial intelligence (AI) is revolutionizing production processes and optimizing efficiency like never before. By harnessing the power of AI, manufacturers can achieve higher levels of productivity, improve product quality, and reduce costs. The integration of AI into manufacturing operations is paving the way for the future of production.
Improved Predictive Quality Control
One of the key ways AI is transforming manufacturing is through predictive quality control. Traditionally, quality control has relied on manual inspections and sampling, which can be time-consuming and prone to human error. However, AI-powered systems can analyze vast amounts of data in real-time to identify patterns and anomalies, allowing manufacturers to detect and address quality issues before they become major problems.
By continuously monitoring production processes and analyzing data from sensors, cameras, and other sources, AI algorithms can identify deviations from expected norms and automatically trigger corrective actions. This proactive approach to quality control helps manufacturers reduce defects, minimize rework and scrap, and ensure consistent product quality.
Optimized Maintenance and Asset Management
In addition to predictive quality control, AI is also revolutionizing maintenance and asset management in the manufacturing industry. Traditional maintenance practices are often based on fixed schedules or reactive repairs, which can be inefficient and costly. AI-powered systems, on the other hand, enable predictive maintenance by analyzing data from sensors and machines to identify signs of potential equipment failure.
With AI algorithms continuously monitoring the performance of machinery, manufacturers can detect early warning signs of equipment degradation or malfunctions. This allows them to schedule maintenance activities proactively, optimizing uptime and minimizing unplanned downtime. By avoiding costly breakdowns and reducing the need for unscheduled repairs, manufacturers can improve productivity and extend the lifespan of their assets.
Benefits of AI in Manufacturing
- Increased productivity
- Improved product quality
- Reduced costs
- Enhanced safety
- Optimized resource allocation
Overall, the integration of AI into manufacturing processes is transforming the industry and shaping the future of production. By leveraging AI-powered predictive quality control and optimized maintenance practices, manufacturers can achieve higher levels of efficiency, reduce costs, and deliver superior products to their customers.