In recent years, there has been a significant advancement in the field of Artificial Intelligence (AI) and Augmented Reality (AR). These technologies have become increasingly popular and have the potential to enhance virtual experiences in various fields such as gaming, education, healthcare, and...
Latest Innovations in Robot Dexterity for Industrial Automation
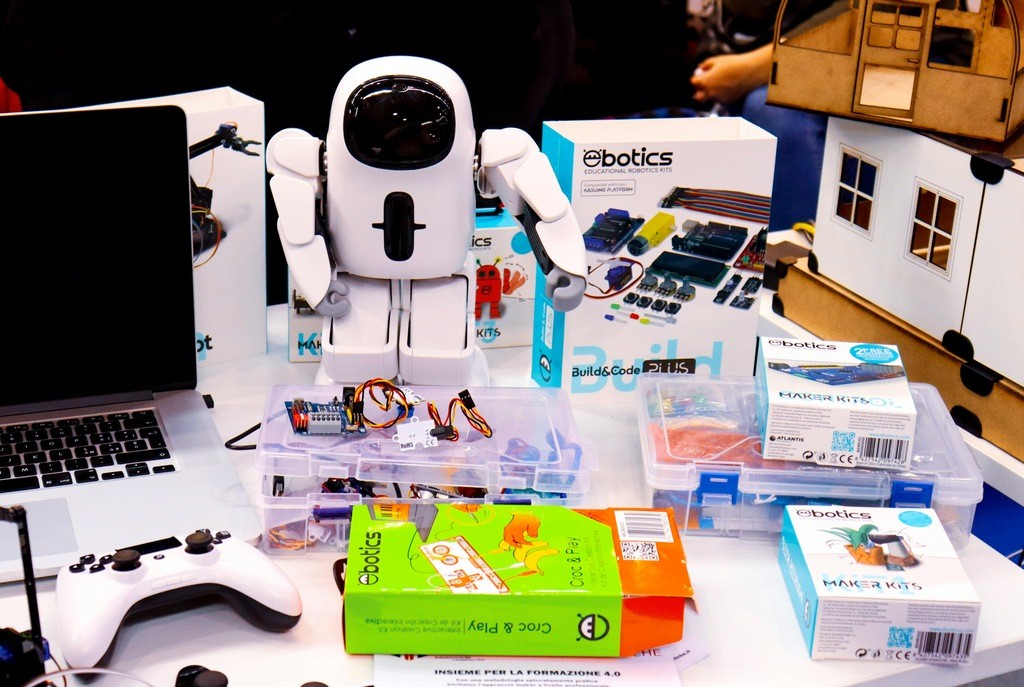
In recent years, there have been significant advancements in the field of robot dexterity for industrial automation. Robots are no longer limited to repetitive tasks on assembly lines; they are now capable of performing complex and delicate operations with precision and efficiency. These innovations in robot dexterity have opened up new possibilities for industries to automate processes that were previously considered too challenging or dangerous for robots.
One of the key innovations in robot dexterity is the development of advanced grippers and end effectors. These devices mimic the human hand and allow robots to manipulate objects with a high degree of flexibility and sensitivity. They can grasp and handle objects of different shapes, sizes, and materials, enabling robots to perform tasks that require fine motor skills, such as assembling small electronic components or packaging fragile items.
Another major breakthrough in robot dexterity is the integration of artificial intelligence and machine learning algorithms. These technologies enable robots to learn and adapt to new tasks and environments, making them more versatile and efficient. By analyzing data and feedback from sensors, robots can optimize their movements and improve their accuracy, reducing errors and increasing productivity. This ability to learn and improve over time is crucial for robots to handle complex tasks that require constant adaptation and problem-solving.
Furthermore, advancements in tactile and force sensing technology have greatly enhanced robot dexterity. Robots equipped with sensors can now perceive and respond to changes in their environment, such as variations in pressure, texture, or temperature. This allows them to handle delicate objects without damaging them and adjust their grip or force based on the task requirements. These tactile sensing capabilities enable robots to perform tasks that previously required human touch and sensitivity, such as picking and placing items in a warehouse or performing intricate surgical procedures.
In conclusion, the latest innovations in robot dexterity for industrial automation have revolutionized the capabilities of robots in performing complex and delicate operations. With advanced grippers, artificial intelligence, and tactile sensing technology, robots can now handle tasks that were once considered challenging or impossible. These advancements not only improve efficiency and productivity in industries but also enhance workplace safety by automating hazardous or repetitive tasks. As we continue to push the boundaries of robot dexterity, we can expect further advancements that will reshape the future of industrial automation.
Advancements in Robot Dexterity for Industrial Automation
In recent years, there have been significant advancements in the field of robot dexterity for industrial automation. These innovations have revolutionized the way tasks are performed in manufacturing and other industries, leading to increased efficiency and productivity.
One of the key advancements in robot dexterity is the development of advanced sensors and perception systems. These sensors enable robots to have a better understanding of their environment, allowing them to adapt to changes and perform tasks with precision. For example, robots can now use 3D vision systems to recognize and manipulate objects of varying shapes and sizes, making them more versatile and capable of handling complex tasks.
Another important advancement is the improvement in robot control algorithms. These algorithms determine how a robot moves and interacts with its surroundings. With the use of advanced control algorithms, robots can now perform delicate and intricate tasks with greater accuracy. This has opened up new possibilities for automation in industries such as electronics assembly, where precision is crucial.
Furthermore, the development of collaborative robots, also known as cobots, has been a game-changer in industrial automation. These robots are designed to work alongside humans, assisting them in tasks that require strength, precision, or repetitive actions. Cobots are equipped with sensors that allow them to detect human presence and adjust their movements accordingly, ensuring safety in the workplace.
Additionally, advancements in robot grippers have contributed to improved dexterity. Grippers are the end-effectors that robots use to grasp and manipulate objects. Traditional grippers were rigid and could only handle specific objects. However, the development of flexible grippers, such as soft robotic grippers, has enabled robots to handle a wider range of objects with varying shapes and sizes. This flexibility has greatly enhanced their dexterity and expanded their applications in industrial automation.
In summary,
Advancements in robot dexterity for industrial automation have been driven by the development of advanced sensors, improved control algorithms, the introduction of collaborative robots, and the evolution of robot grippers. These innovations have transformed the capabilities of robots, allowing them to perform complex tasks with precision and work alongside humans in a safe and efficient manner. As technology continues to advance, we can expect further enhancements in robot dexterity, leading to even greater automation possibilities in the future.
Intelligent Robotic Arms for Precise Operations
One of the latest innovations in robot dexterity for industrial automation is the development of intelligent robotic arms. These advanced robotic arms are designed to perform precise operations with a high level of accuracy and efficiency.
Intelligent robotic arms are equipped with advanced sensors and algorithms that enable them to perceive and understand their environment. These sensors can detect and measure various parameters such as force, torque, position, and orientation. By analyzing this data in real-time, the robotic arms can adapt their movements and responses accordingly.
These robotic arms are also equipped with advanced grippers and end effectors that are designed to handle different types of objects and materials. The grippers can be customized to provide the right amount of force and grip for each specific task. This enables the robotic arms to handle delicate and fragile objects with precision and care.
Furthermore, intelligent robotic arms are integrated with artificial intelligence (AI) algorithms that enable them to learn and improve their performance over time. They can analyze past operations, identify patterns, and optimize their movements and actions accordingly. This allows them to become more efficient and effective in performing repetitive tasks.
The use of intelligent robotic arms in industrial automation has several benefits. Firstly, they can significantly increase productivity and efficiency in manufacturing processes. By performing tasks with precision and speed, they can reduce errors and improve overall production output.
Secondly, intelligent robotic arms can enhance workplace safety by performing tasks that are dangerous or hazardous for human workers. They can handle toxic chemicals, work in extreme temperatures, and operate in confined spaces without putting human operators at risk.
Lastly, these robotic arms can also improve product quality by ensuring consistent and accurate operations. They can perform tasks with a high level of repeatability, minimizing variations and defects in the final products.
In conclusion, intelligent robotic arms are a significant advancement in robot dexterity for industrial automation. With their advanced sensors, grippers, and AI algorithms, they can perform precise operations with efficiency, safety, and high-quality results. These robotic arms have the potential to revolutionize various industries and drive the future of automation.
Cutting-Edge Grippers for Enhanced Handling
Grippers are an essential component of robotic systems used in industrial automation. They are responsible for picking up and manipulating objects with precision and accuracy. In recent years, there have been significant advancements in gripper technology, leading to the development of cutting-edge grippers that offer enhanced handling capabilities.
One of the latest innovations in grippers is the incorporation of tactile sensors. These sensors enable the gripper to have a better understanding of the object it is handling. By providing feedback on the object's shape, texture, and hardness, the gripper can adjust its grip accordingly. This allows for more efficient and secure handling, especially when dealing with delicate objects or irregularly shaped items.
Another breakthrough in gripper technology is the use of adaptive fingers. These fingers are designed to conform to the shape of the object being handled, ensuring a secure grip. By adjusting their position and shape in real-time, adaptive fingers can handle objects with varying geometries and sizes, eliminating the need for specific gripper designs for each object. This not only simplifies the setup process but also increases the flexibility and versatility of the robotic system.
Furthermore, there have been advancements in the field of soft grippers. Soft grippers are made of flexible materials that can deform and conform to the shape of the object. This allows them to handle objects with complex geometries or fragile surfaces without causing damage. Soft grippers are particularly useful in industries such as food processing and electronics assembly, where gentle handling is crucial.
In addition to these innovations, there have also been developments in the area of collaborative grippers. Collaborative grippers are designed to work safely alongside human operators, without the need for protective barriers. These grippers are equipped with force and torque sensors, as well as advanced control algorithms, which allow them to detect and respond to the presence of humans. This enables human-robot collaboration, where robots can assist humans in tasks that require strength or precision.
Gripper Innovations and Benefits:
- Tactile Sensors: Improved grip adjustment and handling of delicate objects
- Adaptive Fingers: Secure grip on objects with varying geometries and sizes
- Soft Grippers: Gentle handling of objects with complex geometries or fragile surfaces
- Collaborative Grippers: Safe human-robot collaboration without protective barriers
In conclusion, the latest innovations in gripper technology have revolutionized the field of industrial automation. With the incorporation of tactile sensors, adaptive fingers, soft materials, and collaborative capabilities, these cutting-edge grippers offer enhanced handling capabilities, leading to increased productivity, efficiency, and safety in robotic systems.